I. Definition and Generation of Sludge
-
Definition
Sludge refers to semi-solid or solid residues generated during wastewater treatment. It consists of organic debris, bacterial biomass, inorganic particles, colloids, and other substances, characterized by high moisture content (initial ≥99%), high organic content, and biodegradability. According to the Water Pollution Prevention and Control Law, sludge is classified as a byproduct of wastewater treatment, excluding screenings, scum, and grit.
-
Sources
- Pretreatment (e.g., screens, grit chambers) produces screenings and grit.
- Primary Treatment (primary sedimentation tanks) generates primary sludge.
- Secondary Treatment (biological reactors, secondary clarifiers) yields activated sludge.
- Tertiary Treatment (chemical coagulation, filtration) produces chemical sludge.
- Wastewater Types: Includes municipal, industrial, and water supply sludge.
- Yield: 5–10 tons of sludge per 10,000 tons of wastewater (at 80% moisture content), depending on influent quality and treatment processes.
- Composition and Risks
Sludge contains pathogens, heavy metals (e.g., lead, cadmium), persistent organic pollutants, and other contaminants. Improper handling may lead to secondary pollution (eutrophication, heavy metal leaching).
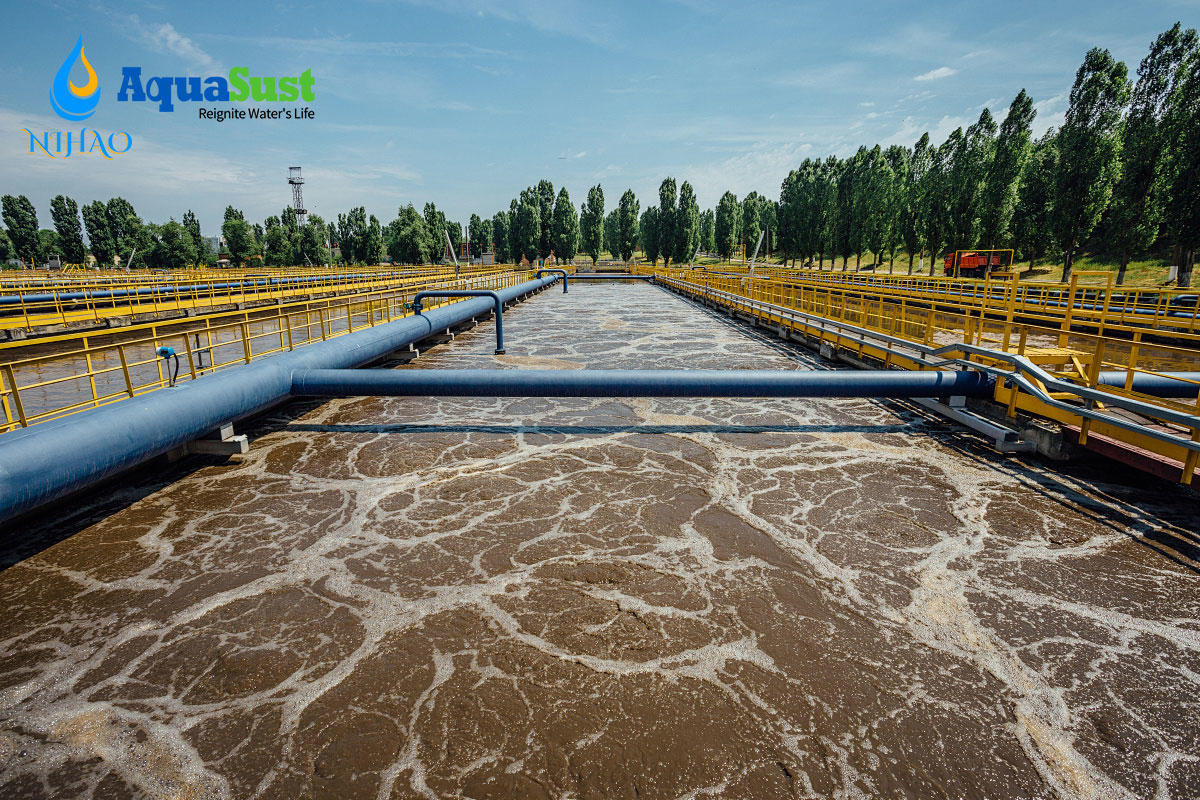
II. Key Sludge Removal Methods and Processes
The core objectives are volume reduction, stabilization, harmlessness, and resource recovery. Key stages include thickening, dewatering, stabilization, drying, and final disposal.
- Thickening
- Purpose: Remove interstitial water to reduce volume (moisture content from 99% to 94–97%).
- Technologies:
Method |
Advantages |
Limitations |
Gravity Thickening |
Low energy, simple operation |
Large footprint, phosphorus release |
Flotation |
Suitable for dilute sludge |
High energy consumption |
Centrifugal |
High efficiency, compact |
High capital and maintenance costs |
- Dewatering
- Purpose: Reduce moisture content to 65–80% for easier transport.
- Technologies:
- Mechanical Methods: Belt filter presses (for activated sludge), plate-and-frame filter presses (moisture ≤60%), centrifuges (continuous operation).
- Natural Drying: Climate-dependent, low cost for small plants.
- Case Study: Shanghai Bailonggang Sludge Project uses high-pressure diaphragm filter presses, treating 1,500 tons/day; dewatered sludge is landfilled or incinerated.
- Stabilization
- Purpose: Degrade organics, reduce odors, and pathogens.
- Methods:
- Anaerobic Digestion: Produces biogas (50–70% methane) but requires airtight systems.
- Aerobic Composting: Converts sludge into humus for agriculture.
- Lime Stabilization: Quick pathogen inactivation but increases sludge weight.
- Drying
- Purpose: Achieve 10–40% moisture content for resource recovery.
- Technologies:
Method |
Advantages |
Limitations |
Thermal Drying |
High volume reduction (90%) |
High energy, odor emissions |
Solar Drying |
Low-carbon, low cost |
Climate-dependent, slow |
Microwave |
Fast and uniform drying |
High equipment costs |
- Final Disposal
- Landfilling: Simple but requires strict standards (moisture ≤60%, organics ≤5%) and risks leachate generation.
- Incineration: Complete volume reduction (10% ash residue) but needs exhaust treatment.
- Land Application: Composted sludge for soil improvement, subject to heavy metal limits.
- Material Reuse: Sludge bricks (e.g., Guangdong Heyuan project produces 36,000 bricks/year)
III. Technology Comparison
Stage |
Technology |
Pros |
Cons |
Thickening |
Gravity |
Low energy, simple |
Large footprint, phosphorus release |
|
Centrifugal |
High efficiency |
High cost |
Dewatering |
Plate-and-Frame |
Low moisture (≤60%) |
Batch operation, complex maintenance |
|
Belt Press |
Continuous processing |
High chemical use, secondary pollution |
Stabilization |
Anaerobic Digestion |
Biogas recovery, 30–50% reduction |
High investment, airtight systems needed |
|
Lime Stabilization |
Rapid pathogen kill |
Weight increase, higher costs |
Drying |
Solar |
Low-carbon |
Climate-dependent |
|
Thermal |
Fast, efficient |
High energy use |
Disposal |
Incineration |
Complete harmlessness |
Dioxin risks, high costs |
|
Land Application |
Resource recovery |
Heavy metal restrictions |
IV. Real-World Applications
- Jinjiang Sludge Disposal Center (China):
- Uses "back-pressure steam turbine + waste heat drying," processing 180,000 tons/year and producing 36,000 bricks/day.
- Shanghai Bailonggang Project:
- Asia’s largest sludge facility; high-pressure dewatering to 40% moisture, with sludge used for landfill/incineration.
- Chongqing Gasification Project:
- Employs fluidized bed gasification to convert 100 tons/day of sludge into steam and electricity.
V. Emerging Technologies
- Pyrolysis/Carbonization: Converts sludge to biochar for soil remediation or fuel (energy-intensive).
- Ultrasonic Treatment: Enhances dewatering via cavitation (often combined with other methods).
- Plasma Technology: High-temperature decomposition (zero secondary pollution; used in Sweden/Japan).
- Bioelectrochemical Systems: Microbial degradation with electricity generation (lab-scale).
VI. Challenges and Recommendations
- Technical Barriers: High chemical use (e.g., polyacrylamide), energy-intensive drying.
- Policy Needs: Strengthen sludge recycling standards (e.g., Technical Guidelines for Sludge Treatment) and promote ash reuse in construction.
- Cost Optimization: Encourage co-processing with power/cement plants to reduce costs.